

High nickel in NMC materials accounted for more than half, and mainly for Japan and South Korea in the production of enterprises, nickel market share is limited; spray pyrolysis such as the ultimate cost reduction, it is possible to realize the NMC materials to capture the market of LFP, nickel single crystal to capture the market of high-nickel secondary ball market.
Leach:LiNi0.6Co0.1Mn0.3O2+3HNO3=LiNO3+Ni0.6Co0.1Mn0.3(NO3)2+O2↑
Pyrolysis:Ni0.6Co0.1Mn0.3(NO3)2+LiNO3=Ni0.6Co0.1Mn0.3O-LiO+3NO2↑+0.5O2↑
Acid production:4NO2+2H2O+O2↑=4HNO3
Spray Principle
Acid removal treatment system
Acid removal system
√ The NO3 root acts only as a carrier in the whole process and is not produced or consumed!
Co-precipitation principle
Leach:LiNi0.6Co0.1Mn0.3O2+1.5H2SO4=0.5Li2SO4+Ni0.6Co0.1Mn0.3SO4+0.25O2↑+1.5H2O Sodium soap:2H-R organic phase+2NaOH→2NaR has+2H2O
Extract:2NaR organic phase+MSO4→M(R organic phase)2+Na2SO4
Back extract:M(R organic phase)2+H2SO4→2HR organic phase+MSO4
Precipitate:Ni0.6Co0.1Mn0.3SO4+2NaOH=Na2SO4+Ni0.6Co0.1Mn0.3(OH)2
×The production of one equivalent of metal solution requires the consumption of 4 equivalents of NaOH and 2.5 equivalents of H2SO4.
Spray Pyrolysis Theory
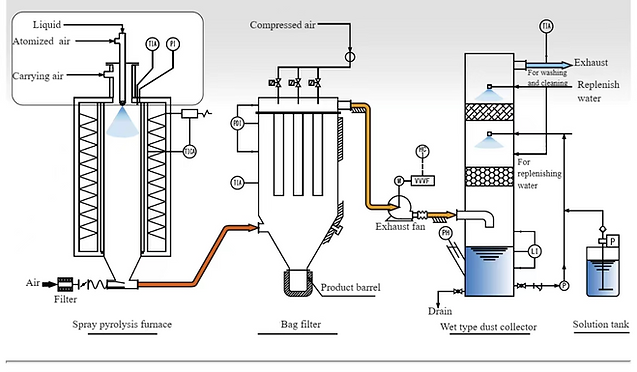
Ni0.6Co0.1Mn0.03(NO3)2
HNO3 de-waste water
Step 1 Pyrolysis Step 2 Acid production
√ Short process: two-step method to prepare oxide precursors
√ Low auxiliary materials: liquid alkali, ammonia water, nitrogen are no longer required
√ Zero emissions: no water treatment solid investment costs, low operating costs for pyro processes

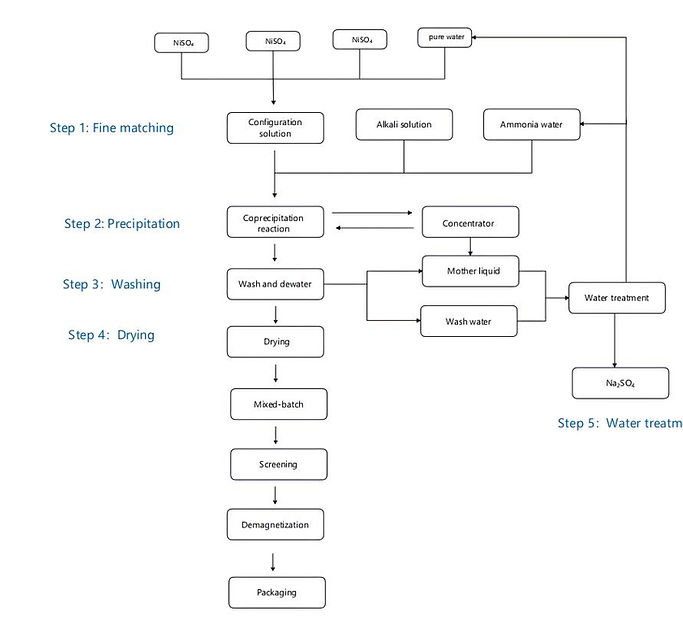.jpg)

Equipment components
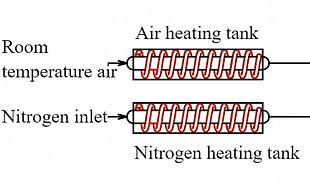
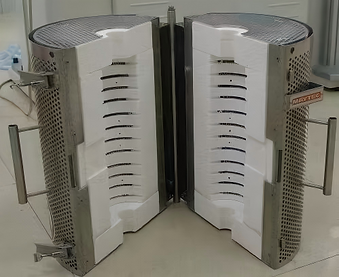.png)
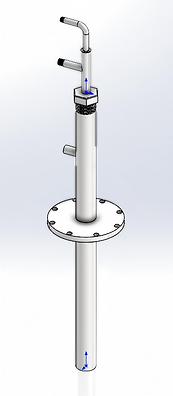.png)
Feed port
Air inlet
Nitrogen inlet
Temperature of pressurized air and nitrogen: 200°C
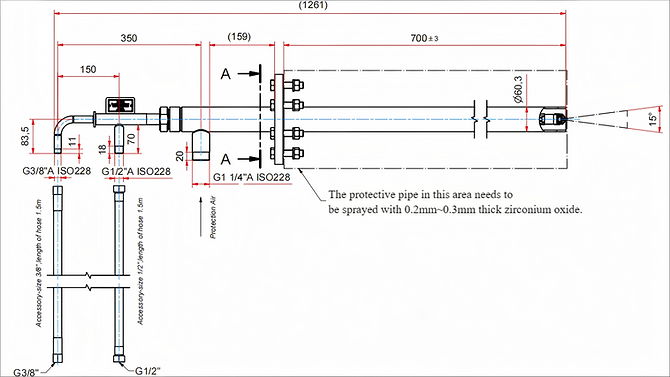




Reuse HNO3
Battery powder
Reduction roasting
Leaching and removaling impurity
Extraction
Evaporation and production
Products
Nickel sulfate crystals
Cobalt sulfate crystals
Manganese sulfate crystals
Yield 99%
Traditional recycling process
First wave of wet process cost reduction
Lithium carbonate crystals
Yield 90%
Battery powder
Reduction roasting
Leaching and removaling impurity
Products
New recycling process
Mixed solution of nickel/cobalt/manganese/
lithium salts
Yield 99%
Liquid alkali
Ammonia water, nitrogen
Pure water
Lithium salt
Raw materials
Liquid preparation
Precipitation reaction
Aging
Centrifugal washing
Drying
Hydroxide precursor
High mixing
Raw materials: nickel sulfate, cobalt sulfate, manganese sulfate
Sodium sulfate high-salt wastewater
Primary sintering
Coating agent
Crushing
Coating
Secondary sintering
Screening and demagnet-ization
Finished products
The second wave of precursor cost reduction
Conventional co-precipitation precursor NMC cathode material process
The third wave of sintering cost reduction。
Raw material ①: Lithium-containing solution
Acid and water recycling
Coating agent
Raw materials
Dissolution and impurity removal
Spray pyrolysis
Primary sintering
Crushing and demagnetization
Lithium-containing hydride precursor
Coating
Secondary sintering
Screening and demagnet-ization
Finished products
Raw materials②: Nickel salt/cobalt salt prepared by NPI/MHP, recycled nickel/cobalt/manganese/lithium metal mixture
New spray pyrolysis precursor NMC cathode material process
Sources of raw materials: 1 Clean waste materials from cathode factories, fan materials/screen materials, etc.; 2 Clean pole piece materials from battery cell factories; 3 For example, a large battery of a certain model of a certain model retired by NIO/Liang Li after 5 years, the cathode sheets will be automatically disassembled by molds and black powder will be collected. In the future, the trend of charged overall crushing should be applicable to small batteries of unknown brands, and refined disassembly will be the mainstream.
1 The pyrolysis lithium precursor has achieved atomic-level mixing. Can the cumbersome process of multiple crushing, mixing and sintering be eliminated?
2 If the residence time of pyrolysis with lithium precursor in the pyrolysis furnace is increased as much as possible, is it possible to build up the crystalline form by subsequent sintering only once?
3 The current atomization technology pyrolyzes lithium precursors with a size of 50 microns (atomization 200 microns), which are hollow inside and need to be crushed by air flow grinding before sintering. Is it possible to achieve a lithium precursor with a size of 4 microns (atomization 16 microns)?
4 If we directly obtain a 4-micron lithium precursor, can we directly sinter it in the back end without cooling it down to save energy?
5 The reason why the primary sintering is so hard is because of the solid melting of lithium carbonate. Is it possible to bring the lithium precursor into the rotary kiln for low-temperature shaping without causing hardening? There is no need for subsequent crushing, and there is no water vapor and residual alkali. The stainless steel cylinder can be used. The long low-temperature shaping time can make up for the problem of discharging materials in sequence.
1. 6 series monocrystalline cathode material sales price of about 15w per ton, from the black powder to the cathode of the whole process of the old process needs nearly RMB50,000 , the new process is expected to RMB15,000 .
2. The old process of the whole process tons of solid investment is expected to 900 million; the new process of the whole process is expected to solid investment 450 million.
Spray pyrolysis of 6-series single crystal precursors - typical values
.jpg)
.jpg)
Materials after sintering
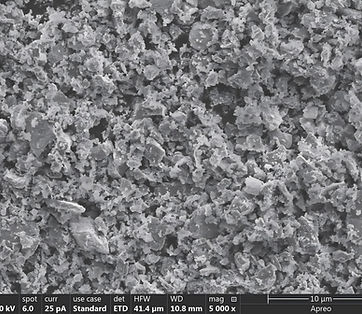.jpg)
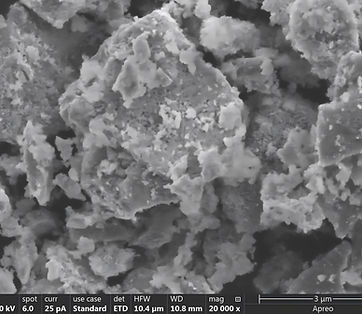.jpg)
Materials after crushing
Verification of 6-series single crystal precursor by spray pyrolysis

★ Basf-SS verification

Passed XTC internal verification; Capacity is 1mah/g lower, residual lithium is relative high
★ BTR has passed CATL and LG ton-level verification!
Core Technology


In-depth analysis and improvement of spray headatomization effect, heat resistance, wear resistance and acid resistance

Independently design internal temperature field

99.8% recovery of acid